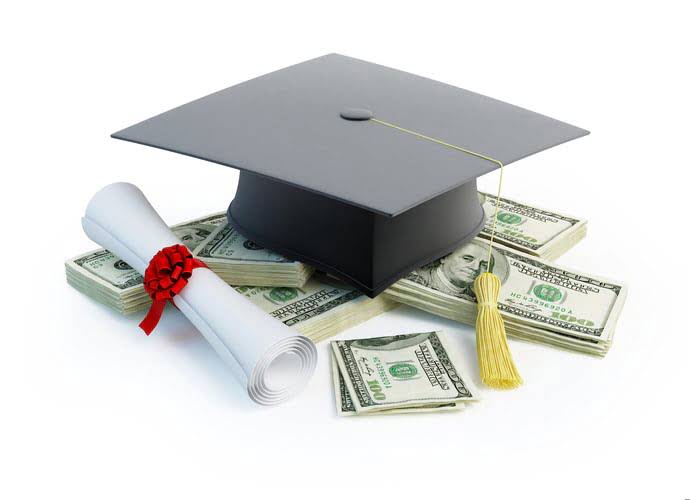
Having a clear returns policy and making the process fast and easy for the customer is essential. By keeping the cost per unit low, you can pass on the savings to the customer and entice more customers to buy (or take home more money if you’re able to sell it at a premium). While Greg can mark up the price of his candles (charging customers more than his competitor), he knows he should identify ways to reduce his costs to have a healthier margin. This same approach can be used to predict costs for service and merchandising firms, as shown by examining the costs incurred by J&L Accounting to prepare a corporate income tax return, shown in Table 2.10. Let’s take a more in-depth look at the cost equation by examining the costs incurred by Eagle Electronics in the manufacture of home security systems, as shown in Table 2.9.
Making a profit selling products is the foundation of any successful ecommerce business. If you know what sales volumes to anticipate, you can manage your inventory accordingly to reduce costs. Our end-to-end supply chain solutions also improve inbound and outbound logistics, including warehouse receiving, to establish a more efficient, cost-effective supply chain. ShipBob’s fast-growing fulfillment network helps you save on costs when storing inventory in our fulfillment centers by only paying for the space you need.
How to calculate cost per unit
Understanding the various labels used for costs is the first step toward using costs to evaluate business decisions. You will learn more about these various labels and how they are applied in decision-making processes as you continue your study of managerial accounting in this course. Fixed costs are spread across all units, thus, for many offerings, the greater the number of units, the lower the average cost. It helps you amplify the SKU (stock-keeping units), which are your highest profit generators, and assists in boosting customer loyalty and satisfaction. Whether it’s a slow-selling item or obsolete inventory, having an inventory management system in place can enhance visibility so you can make wise decisions about your product catalog sooner than later. As far as returns go, 92% of shoppers say they will buy again if the returns process was easy and overall positive.
- Understanding how unit costs change as output changes – and over time – is very useful for a business.
- Because the trend line is somewhat subjective, the scatter graph is often used as a preliminary tool to explore the possibility that the relationship between cost and activity is generally a linear relationship.
- They know what their costs were for June, but now they want to predict their costs for July.
- Calculating cost per unit is important because it is a key determinant of net profit per unit or earnings per share (EPS).
- These measures will help in space rationalisation and price optimisation with the key goal of improving cash flows, increasing return on invested capital, and boosting operating margins.
- Spending less money on material costs, which tend to account for a majority of production costs, can obviously reduce cost per unit.
- It is a crucial measure for businesses to determine their profitability and analytical capabilities.
Here is how ShipBob can turn your logistics operations into a revenue driver. Instead of having to handle all SKU management and logistics on your own, you can outsource it to ShipBob and save time, energy, and money. One-fourth of online customers return 5-15% of what they purchase, and the retail industry loses about $50 billion in the form of deadstock per year. Dummies has always stood for taking on complex concepts and making them easy to understand. Dummies helps everyone be more knowledgeable and confident in applying what they know. Whether it's to pass that big test, qualify for that big promotion or even master that cooking technique; people who rely on dummies, rely on it to learn the critical skills and relevant information necessary for success.
Accounting and Accountability
If the costs (and subsequent sales) don’t justify supporting a particular product, then it’s time to discontinue it. In terms of salaries, rent, and other overhead, their monthly fixed cost of production https://www.bookstime.com/articles/construction-in-progress-accounting is $5,000. Any expense incurred in the storage of unsold inventory is referred to as holding costs. These costs can range from warehousing to labour costs, to depreciation and opportunity costs.
- Dead stock can be costly for businesses, as they have to pay for the cost of storing it, as well as the cost of eventually disposing of it.
- Additionally, the unit cost is influenced by multiple factors, such as fixed costs, variable costs, direct and indirect costs, production volume, and more.
- ShipBob also helps your online business with tracking distribution metrics and inventory management KPIs so you can easily make cost-conscious supply chain decisions.
- While the cost per unit refers to how much you spend to deliver one unit, the price per unit refers to how much you charge customers for each item sold.
- Making a profit selling products is the foundation of any successful ecommerce business.
In addition to the equivalent units, it is necessary to track the units completed as well as the units remaining in ending inventory. A similar process is used to account for the costs completed and transferred. Reconciling the number of units and the costs is part of the process costing system. The reconciliation involves the total of beginning inventory and units started into production. Where Y is the total mixed cost, a is the fixed cost, b is the variable cost per unit, and x is the level of activity.
Step 6 – Apply the Formula on All the Rows
By exploring alternative materials, reducing scrap and waste, and negotiating better pricing with their suppliers, brands can lower material costs and reduce cost per unit. Dealing with these common inventory challenges can hike up logistics costs, from higher storage costs to returns management (e.g., shipping labels, processing how to calculate cost per unit and restocking). The number of units sold within a specific period of time can also impact these costs. Examples are production costs, customer acquisition, packaging, and shipping costs. Spending less money on material costs, which tend to account for a majority of production costs, can obviously reduce cost per unit.
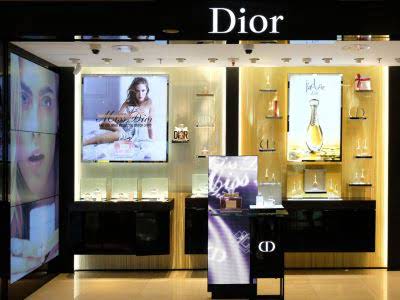